Understanding Lathe Machine Parts and Their Role in Metal Fabrication
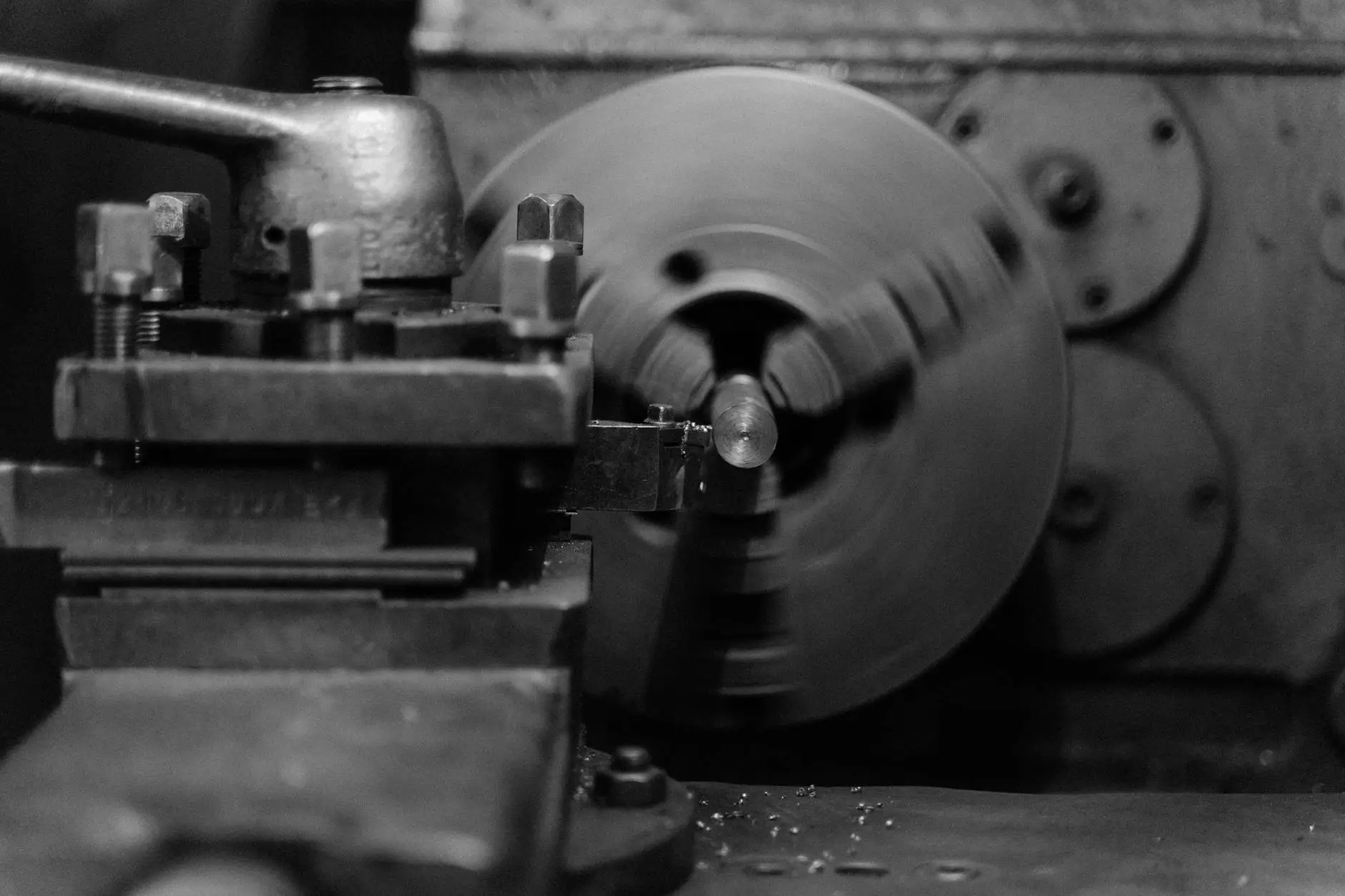
In the world of metal fabrication, lathe machines play a crucial role in shaping and finishing metal components. The intricate parts of these machines are designed to work together seamlessly, delivering precision and efficiency. In this comprehensive guide, we will delve into the various lathe machine parts, their functions, and their significance in the manufacturing process.
What is a Lathe Machine?
A lathe machine is a versatile tool used primarily for turning, drilling, and finishing materials such as metal, wood, and plastic. It operates by rotating the workpiece against a cutting tool, allowing for precise shaping and dimensional accuracy. The core functionality of a lathe is heavily reliant on its components, each designed to perform specific tasks with utmost efficiency.
Core Components of Lathe Machines
The lathe machine comprises several essential parts, each contributing to its overall functionality. Understanding these parts is vital for optimizing performance in metal fabrication. Here are the primary components:
- Bed: The bed is the heavy base of the lathe that supports the entire structure. It ensures stability and alignment during operation.
- Headstock: Located at the left end, the headstock houses the main motor and controls the spindle's speed and direction.
- Spindle: The spindle is a rotating shaft that holds and drives the workpiece. It is powered by the motor and determines the cutting speed.
- Tailstock: Positioned at the opposite end of the headstock, the tailstock supports the other end of the workpiece and can be adjusted for length.
- Carriage: The carriage moves along the bed and holds the cutting tool. It can be adjusted for depth and angle of cut.
- Cross Slide: Part of the carriage, the cross slide allows for lateral movement of the cutting tool, enhancing the precision of cuts.
- Tool Post: The tool post secures the cutting tools and allows for quick changes between different tools.
The Importance of Lathe Machine Parts in Metal Fabrication
Understanding the functionality of individual lathe machine parts is essential for ensuring optimal efficiency in metal fabrication. Let’s explore the significance of each part in facilitating smooth operations:
1. Bed
The bed of the lathe machine is pivotal in maintaining precision. A well-constructed bed minimizes vibrations during operation, which can lead to inaccuracies. For businesses like DeepMould.net, investing in high-quality lathe machines with a robust bed structure ensures that metal components are manufactured to exact specifications.
2. Headstock
The headstock's ability to control spindle speed directly affects the machining process. Higher speeds are suitable for softer materials, while lower speeds are ideal for harder metals. Understanding how to adjust the headstock can significantly impact production rates and material quality.
3. Spindle
The spindle's reliability is essential for consistent operation. It should be maintained properly to avoid wear and tear, which can compromise workpiece accuracy. Businesses must ensure that spindles are regularly lubricated and checked for alignment.
4. Tailstock
The tailstock provides added support, particularly for longer workpieces. Proper adjustment of the tailstock is necessary to prevent workpiece deflection, which can lead to errors in cutting. Familiarity with its operation can greatly enhance fabrication accuracy.
5. Carriage
The carriage’s movements allow for multidisciplinary machining operations, from turning to tapering to facing. Understanding the intricacies of carriage movement can lead to more complex shaping tasks, expanding a business's capabilities.
6. Cross Slide
With the cross slide, metalworkers can achieve finer detail in their work. This part is crucial for operations requiring intricate contours and detailed finishes, enabling businesses to cater to various client needs.
7. Tool Post
The tool post's design influences how quickly and effectively tools can be changed during production. A well-designed tool post can cut downtime significantly, increasing overall productivity.
Maintaining Lathe Machine Parts for Optimal Performance
Regular maintenance of lathe machine parts is essential for prolonging their lifespan and ensuring consistent performance. Here are some maintenance tips:
- Regular Lubrication: Keeping the moving parts lubricated reduces friction and wear.
- Alignment Checks: Regularly check the alignment of the spindle and tailstock to avoid inaccuracies.
- Cleaning: Frequent cleaning removes debris and metal shavings that can interfere with operations.
- Inspect for Wear: Regular inspections can help identify worn-out parts before they cause a breakdown.
- Calibration: Regular calibration of the machines ensures that measurements remain accurate.
Innovations in Lathe Machine Technology
The advancement of technology has led to the development of sophisticated lathe machines that incorporate features such as CNC (Computer Numerical Control). These innovations enhance precision and allow for complex designs that would be challenging with traditional methods.
The Role of CNC in Modern Lathe Operations
CNC machines automate the movement of the lathe's components, allowing for higher precision and repeatability. This technology reduces the possibility of human error and significantly speeds up the production process. DeepMould.net offers metal fabrication services that leverage the benefits of CNC lathe technology, resulting in superior product quality and quicker turnaround times.
Choosing the Right Lathe Machine Parts for Your Business
When selecting lathe machine parts, businesses must consider several factors that impact performance and productivity:
1. Material Compatibility
Ensure that the lathe parts are compatible with the materials you frequently work with. Different metals require different types of tools and specifications.
2. Vendor Reliability
Choose vendors with a proven track record of supplying quality components. The reliability of parts affects the overall performance of the machine.
3. Cost vs. Quality
While cheaper options may seem appealing, it is essential to consider the long-term implications. Investing in high-quality parts may lead to lower maintenance costs and fewer downtimes.
4. Warranty and Support
Look for suppliers that offer warranties and support. This can provide peace of mind and assistance in case of any issues with the parts.
Future Trends in Lathe Machine Parts and Metal Fabrication
The future of lathe machines and metal fabrication lies in continued innovation. Emerging trends include:
- Smart Manufacturing: Integration of IoT (Internet of Things) for real-time monitoring and maintenance prediction.
- Advanced Materials: Development of new materials for lathe components that enhance durability and performance.
- Automation: Increasing use of robotics and AI to automate machining processes, improving efficiency and safety.
- Sustainability: Striving for eco-friendly manufacturing processes, focusing on reducing waste and energy consumption.
Conclusion: The Vital Role of Lathe Machine Parts in Metal Fabrication
In summary, understanding the intricacies of lathe machine parts is essential for anyone involved in metal fabrication. Each component plays a critical role in the machine's function, directly influencing product quality and operational efficiency. By investing time and resources into maintaining and optimizing these parts, businesses like DeepMould.net can achieve superior results that stand the test of time.
Whether you are a seasoned manufacturer or just starting, embracing advancements in lathe technology and understanding the value of each component will empower you to excel in the competitive landscape of metal fabrication.