Unlocking Opportunities: The Role of Injection Molded Plastics Suppliers in Modern Manufacturing
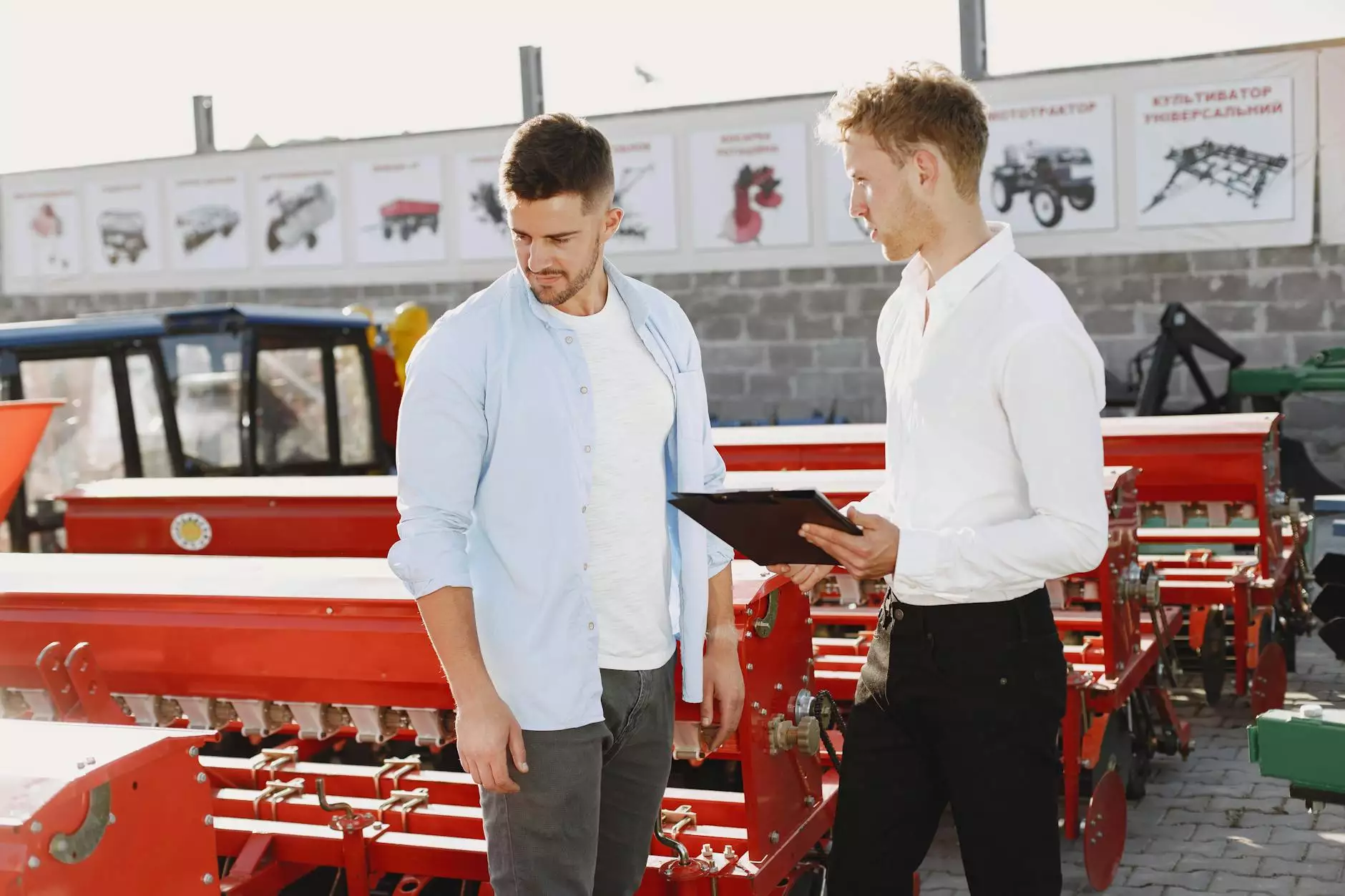
Injection molded plastics suppliers play a critical role in the manufacturing and production sectors, providing essential materials and services that drive innovation and efficiency. With advancements in technology and materials science, businesses have increasingly relied on plastic injection molding for a wide array of applications. In this article, we will explore the intricacies of this process, the benefits it offers, and why companies like Deep Mould stand out as leaders in this essential field.
Understanding Injection Molding: A Closer Look
Injection molding is a manufacturing process that involves the creation of parts by injecting molten plastic into a mold. This technique is revered for its ability to produce complex shapes with high precision and repeatability. The process typically involves several key steps:
- Material Selection: Choosing the right type of plastic resin is crucial, as different materials offer varying properties such as strength, flexibility, and temperature resistance.
- Melting and Injection: The selected resin pellets are heated until they become a flowable liquid and then injected into a mold under high pressure.
- Cooling and Solidification: Once the resin fills the mold, it is cooled, causing it to solidify and take the shape of the mold.
- Mold Removal: After cooling, the mold is opened, and the newly formed part is ejected for further processing or finishing.
The Importance of Quality in Injection Molding
Quality is paramount when it comes to injection molded products. The precision of the mold and the quality of the raw materials directly affect the end product's durability, function, and appearance. Therefore, working with reputable injection molded plastics suppliers is essential for manufacturers aiming for excellence. Poor quality can result in:
- Increased Costs: Defective parts may lead to costly rework or scrap.
- Production Delays: Compromised components can disrupt production schedules.
- Brand Reputation Risks: Delivering inferior products can damage a company's reputation in the market.
Why Choose Deep Mould as Your Injection Molded Plastics Supplier?
Deep Mould is a premier name in the industry, known for its commitment to quality and customer satisfaction. Here are several reasons why your business should consider partnering with us:
1. Expertise in Diverse Industries
Deep Mould serves a myriad of sectors including automotive, consumer goods, healthcare, and more. Our proficiency in various applications means that we understand the unique requirements of each industry and can tailor our services accordingly.
2. State-of-the-Art Facilities
Investing in cutting-edge technology, our manufacturing facilities host advanced injection molding machines capable of producing intricate designs with exceptional precision.
3. Comprehensive Support
Our team of engineers and technicians provides end-to-end support, beginning with design and prototyping, and extending through to final production and quality assurance.
4. Commitment to Sustainability
With a growing awareness of environmental issues, Deep Mould is dedicated to sustainable practices in our manufacturing processes, including recycling initiatives and energy-efficient production techniques.
Exploring Different Types of Injection Molded Plastics
There is a wide range of plastics used in injection molding, each offering distinct advantages:
1. Acrylonitrile Butadiene Styrene (ABS)
ABS is known for its toughness and impact resistance, making it a popular choice for consumer products such as electronics casings and toys.
2. Polypropylene (PP)
Offering excellent chemical resistance and a good balance of mechanical properties, polypropylene is useful in packaging and automotive components.
3. Polyethylene (PE)
Polyethylene is one of the most common plastics used, valued for its flexibility, low-density, and resistance to moisture, making it ideal for containers and bottles.
4. Polystyrene (PS)
Polystyrene is widely utilized in packaging and disposable objects due to its light weight and low production costs.
Key Benefits of Injection Molding
Choosing injection molding for your manufacturing processes comes with numerous benefits:
- Cost Efficiency: High-volume production can significantly lower costs per unit.
- Speed: Injection molding allows for the rapid production of parts, making it suitable for large-scale orders.
- Customization: Molds can be designed for unique specifications, allowing for product differentiation.
- Reduced Waste: The precision of the process minimizes material waste, contributing to sustainability.
Future Trends in Injection Molding
The injection molding industry is constantly evolving. Here are a few trends to keep an eye on:
1. Increased Use of Bioplastics
With the growing demand for sustainable materials, the use of biodegradable and compostable plastics is on the rise.
2. Advanced Automation
Integrating automation and robotics into injection molding processes improves efficiency and reduces labor costs.
3. 3D Printing Innovations
The ability to rapidly prototype molds using 3D printing technology is revolutionizing the design process in injection molding.
Conclusion: Partnering for Success
In conclusion, injection molded plastics suppliers like Deep Mould are essential partners for businesses looking to innovate and elevate their product offerings. With a commitment to quality, sustainability, and advanced technology, we stand ready to meet the challenges of tomorrow’s manufacturing landscape. As the demand for precision and efficiency in plastic parts continues to grow, aligning with a trusted supplier becomes increasingly important. Reach out to us at Deep Mould to learn how we can help your business succeed in today's competitive market.
Visit our website: Deep Mould for more information on our services and to connect with our team of experts.