Low Pressure Casting: Revolutionizing Art Supplies and Product Design
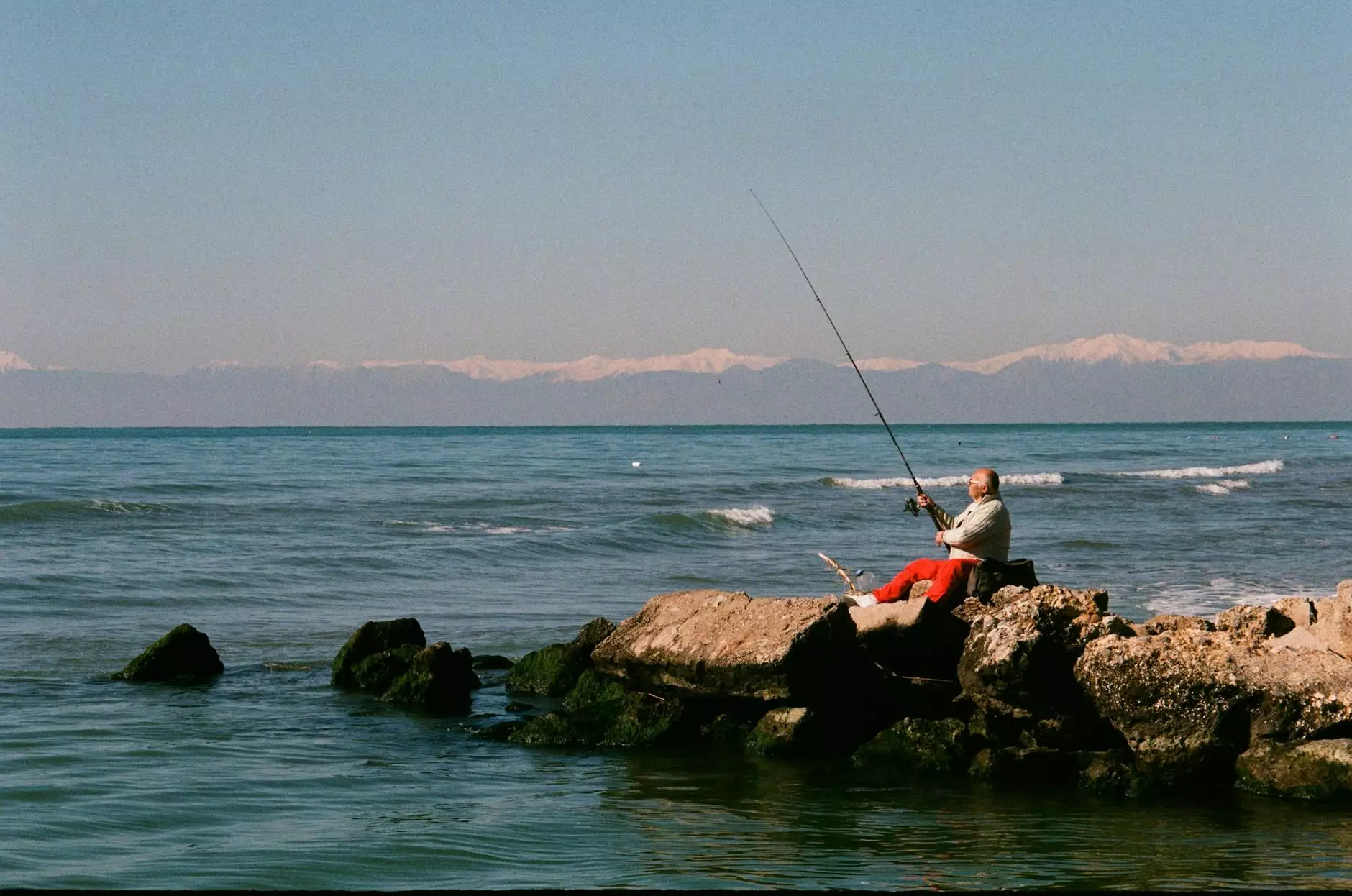
The world of manufacturing and design is rapidly evolving, and low pressure casting is at the forefront of this change. This innovative method is not only enhancing the efficiency and quality in product design but also making significant strides in the fields of art supplies and 3D printing. In this article, we delve deep into the benefits, applications, and future of low pressure casting, aimed at helping businesses and creators unlock new potential.
Understanding Low Pressure Casting
Low pressure casting is a manufacturing process that involves injecting molten metal into a mold under controlled pressure conditions. Unlike traditional high-pressure casting, this method operates at significantly lower pressure, which allows for better fluidity of the metal and improved surface finish. Here are some key characteristics of low pressure casting:
- Efficiency: The process allows for faster cycle times, reducing production costs.
- Precision: Low pressure ensures less turbulence, leading to a more accurate filling of the mold.
- Quality: The resultant castings have fewer defects and superior surface qualities.
Benefits of Low Pressure Casting for Businesses
Adopting low pressure casting methodologies can provide numerous advantages for businesses across different sectors, particularly in art supplies, product design, and 3D printing. Here are some notable benefits:
1. Cost-Effectiveness
One of the most compelling reasons businesses should consider low pressure casting is its cost-effectiveness. By utilizing materials more efficiently and minimizing waste, companies can significantly reduce production costs. Moreover, the durability of the casts means that the initial investment in higher quality molds can be offset by their longevity.
2. Enhanced Creativity in Art Supplies
Artists and creators are always looking for innovative materials to bring their visions to life. Low pressure casting opens new avenues for art supplies by allowing for the production of intricate and detailed components that were previously difficult or impossible to achieve. This includes:
- Custom Art Pieces: Artists can create unique sculptures and artistic forms with complex geometries.
- Sculpting Tools: Manufacturers can produce specialized tools that aid in the creative process.
- Functional Art: The blend of functionality and aesthetic appeal in products can be achieved through tailored designs.
3. Flexibility in Product Design
Low pressure casting allows designers to experiment with different materials such as aluminum, magnesium, and other alloys, giving them the flexibility to choose the best characteristics for their designs. This versatility is critical in product design, where different properties like weight, strength, and corrosion resistance are often essential.
4. Superior Surface Finishing
The inherent properties of low pressure casting facilitate achieving a smoother surface finish, which is particularly beneficial in industries where aesthetics are paramount. This means less time spent on polishing and finishing processes, allowing designers to focus more on creativity and less on post-production work.
The Process of Low Pressure Casting
To better understand how low pressure casting works, let’s break down the key stages of the process:
1. Mold Preparation
The first step involves creating a high-quality mold, typically made from durable materials such as steel or sand. Molds can be designed for single use or multiple production runs, depending on the project requirements. The precision of the mold significantly influences the final product quality.
2. Melting the Metal
In this stage, the chosen metal is heated to its melting point in a furnace. The melting process should be carefully controlled to avoid impurities and ensure a uniform temperature. The type of metal selected often depends on the desired properties of the final product.
3. Vacuum Injection
Once the metal is molten, the typical method involves creating a vacuum that draws the molten metal into the mold cavity. This occurs at a low pressure level, allowing the metal to fill the mold completely and accurately. This step is crucial for reducing air entrapment and ensuring high-quality castings.
4. Cooling and Solidification
After the mold is filled, the molten metal begins to cool and solidify. Depending on the metal type and mold configuration, this process can take anywhere from a few minutes to several hours. The cooling rate can also affect the material properties, and designers can manipulate it to achieve specific characteristics.
5. Finishing Touches
Once the metal has solidified, the next stage involves removing the casting from the mold and performing any additional finishing processes. This might include trimming, polishing, or surface treatments to achieve the desired finish.
Applications of Low Pressure Casting in Various Industries
Low pressure casting is not confined to a single industry; its applications are diverse and impactful across multiple sectors. Let’s explore how various industries benefit from this innovative casting technique:
1. Automotive Industry
The automotive sector has embraced low pressure casting for producing lightweight yet durable components. By using materials like aluminum, manufacturers can create parts that reduce overall vehicle weight, leading to improved fuel efficiency.
2. Aerospace Sector
Aerospace manufacturers require precision parts that meet stringent safety and performance standards. Low pressure casting allows for the production of intricate components that can withstand extreme conditions while minimizing weight, crucial for aircraft performance.
3. Medical Equipment
In the field of healthcare, low pressure casting enables the production of high-quality molds and devices, such as surgical instruments and implants, that require exact specifications for safety and effectiveness.
4. Jewelry Design
Jewelry designers benefit from low pressure casting's precision, allowing them to create intricate designs that highlight both beauty and craftsmanship. This process enables the production of complex jewelry pieces with minimal waste.
Low Pressure Casting in the 3D Printing Era
As the industry leans toward innovation, the intersection of low pressure casting and 3D printing presents exciting possibilities. The two methods can complement each other, allowing for:
- Prototype Production: Rapid prototyping using 3D printing allows designers to create models that can subsequently be cast in high-quality materials.
- Customization: Users can design one-off pieces that can be produced through low pressure casting, allowing for mass customization of products.
- Efficiency: Combining these techniques streamlines production and dramatically reduces lead times.
Future Trends in Low Pressure Casting
The future of low pressure casting is promising, with several trends likely to shape its evolution:
1. Advances in Material Science
As material science continues to advance, expect to see innovations in alloys and composites that enhance the performance and aesthetics of cast components. This will allow designers to create even more complex and lightweight designs.
2. Automation and Smart Manufacturing
With the rise of smart manufacturing technologies and automation, low pressure casting processes may become more sophisticated, leading to increased production efficiency and reduced human error.
3. Sustainable Practices
As industries shift towards sustainability, low pressure casting can be improved to reduce energy consumption and minimize waste in the manufacturing process. Using recycled materials will also become a significant focus.
Conclusion
In summary, low pressure casting represents a transformative technology that holds great potential for businesses in art supplies, product design, and 3D printing. By enhancing efficiency, promoting creativity, and allowing for unparalleled precision, this casting method can significantly impact the way products are designed and manufactured. As this technology continues to develop, it will undoubtedly unlock new possibilities for designers and manufacturers alike.
For businesses looking to thrive in a competitive market, embracing low pressure casting may be the key to unlocking innovative solutions and delivering extraordinary products. Explore this cutting-edge technique and integrate its benefits into your creative process at arti90.com.